第一章 机械加工工艺规程设计
机械加工工艺规程是规定产品或零部件机械加工工艺过程和操作方法等的工艺文件。它体现了生产规模的大小、工艺水平的高低和解决各种工艺问题的方法和手段。
第一节基本概念
一.机械产品生产过程与机械加工工艺过程
(一)生产过程
从原材料到机械产品出厂的全部劳动过程。包括:
1)毛坯的制造
2)原材料的运输和保存
3)生产准备和技术准备
4)零件的机械加工及热处理
5)产品的装配、检验、试车、油漆、包装等。
直接生产过程:
被加工对象的尺寸、形状或性能、位置产生一定的变化。如:零件的机械加工、热处理、装配等。
间接生产过程:
不使加工对象产生直接变化。如:工装夹具的制造、工件的运输、设备的维护等。
(二)机械加工工艺过程
是生产过程的一部分,是对零件采用各种加工方法,直接用于改变毛坯的形状、尺寸、表面粗糙度以及力学物理性能,使之成为合格零件的全部劳动过程。
工艺:使各种原材料、半成品成为成品的方法和过程
工艺过程:在生产过程中,凡是改变生产对象的形状、尺寸、相对位置和性质等,使其成为成品和半成品的过程。
二.机械加工工艺过程的组成
1.工序
一个或一组工人,在一台机床或一个工作地点对一个或同时对几个工件所连续完成的那一部分工艺过程。
划分工序的主要依据:工作地点是否改变和加工是否连续完成。
同一零件,同样的加工内容可以有不同的工序安排。
如图1-1所示的阶梯轴的加工:
图1-1 阶梯轴 |
加工内容:
1.加工小端面2。小端面钻中心孔
3.加工大端面4。大端面钻中心孔
5.车大端外圆6。对大端倒角
7.车小端外圆8。对小端倒角
9.精车外圆
10.铣键槽11。去毛刺
工序方案1:
工序1:加工内容1到9——车床
工序2:加工内容10、11——铣床(手工去毛刺)
工序方案2:
工序1:加工内容1、2、7、8—加工小端
工序2:加工内容3、4、5、6—加工大端
工序3:加工内容9工序4:加工内容10、11
工序方案3:
工序1:加工内容:1、2、3、4—铣两端面打中心孔
工序2:加工内容:5、6、7、8—仿形车外圆、倒角
工序3:加工内容:9—精车外圆
工序4:加工内容:1—铣键槽
工序5:加工内容:11—去毛刺
2.安装
如果在一个工序中要对工件进行几次装夹,则每次装夹下完成的那部分加工内容称为一个安装。
图1-2 工序和安装 |
3.工位
在工件的一次安装中,通过分度(或移位)装置,使工件相对于机床床身变换加工位置,我们把每一个加工位置上的安装内容称为工位。一个安装中可能只有一个工位,也可能有几个工位。
如图1-3为一回转工作台加工孔,钻、扩、铰各为一个加工内容,装夹一次产生一个合格的零件。
该加工共有4个工位:装卸工件、钻孔、扩孔、铰孔,用于依次装夹中
图1-3 多工位回转工作台 |
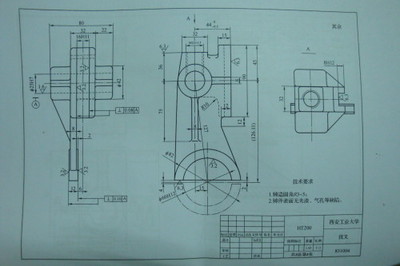
4、工步
指在加工表面不变、切削刀具不变、切削用量不变的情况下所完成的工位内容,称为一个工步。
如上述第二种工序安排,工序1、2各有4个工步
注意:
1)组成工步的任一因素(刀具、切削用量,加工表面)改变后为另一工步。
2)连续进行的若干相同的工步,为简化工艺,习惯看作为一个工步。如一个个加工4-φ10的孔。
3)复合工步
为提高生产率,经常把几个带加工表面,用几把刀具同时进行加工,或采用复合刀具加工表面,采用复合刀具和多刀加工的工步称为复合工步。
5、走刀
切削刀具在加工表面上切削一次所完成的工步内容,称为一次走刀。一个工步可以包括一次或数次走刀。
三.生产类型与机械加工工艺规程
(一)机械加工工艺规程
把比较合理的机械加工工艺过程确定下来,成为施工依据的文件。也就是把工艺过程和操作方法按一定的格式用文件的形式规定下来,成为工艺规程。机械加工的工艺规程的详细程度与生产类型有关,不同的生产类型是由产品的年生产纲领即年产量区别。
(二)生产纲领和生产批量
1.生产纲领:
企业在计划期内,应生产的产品产量和进度计划称为生产纲领,计划期为一年的生产纲领成为年生产纲领。
2.年生产纲领
N=Qn(1+a)(1+b)
Q:产品的年产量(台/年)
n:每台产品中该零件的数量(件/台)
a:备品百分率
b:废品百分率
3.生产批量:
一次投入或产出的同一产品(或零件)的数量
考虑因素:
1)资金周转要快
2)零件加工、调整费用要少
3)保证装配和销售必要的储备量
计算公式:
n:每批中零件数量
N:年生产纲领中规定的零件数量
A:零件应储备的天数
F:一年中工作日天数。
4.生产类型
1)按企业生产专业化程度划分:
(1)大量生产:
同一产品的数量很大,大多数工作地点经常重复的进行同一零件的同一道工序的加工。
(2)成批生产(大批、中批、小批):
一年中分批的制造相同的产品,制造过程有一定的重复性。
(3)单件:
单个生产不同结构和不同尺寸的产品。很少重复。
2)从工艺角度划分:
单件小批生产
中批生产
大批大量生产
3)各种生产类型的工艺特征,如表1-1所示:
表1-1各种生产类型的工艺特点
工艺特征 | 单件小批量 | 中批生产 | 大批大量 |
毛坯 | 自由锻、木模手工造型;精度低、余量大 | 模锻、金属模; 精度和余量中等 | 模锻、机器造型; 精度高,余量小 |
机床 | 通用机床, 机群式布置 | 通用机床,部分专机, 按零件类别分工段排列 | 自动机床,专用机床 生产流水线排列 |
工装 | 通用工装 | 专用工装 | 高效专用工装 |
工艺文件 | 简单工艺过程卡 | 详细工艺过程卡 | 详细工艺过程卡 工序卡、调整卡 |
发展趋势 | 成组技术、数控技术、 加工中心 | 柔性制造系统(FMS) | 计算机集成制造系统 (CIMS),加工自动化 |
(三)机械加工工艺规程的作用
1.工艺规程是生产计划、调度、工人操作、质量检查的依据
2.工艺规程是生产准备(包括技术准备)工作的基础
1)技术关键分析与研究
2)专用工装设计和制造或采购
3)原材料及毛坯的供应
4)设备改造或新设备的购置或定做
3.工艺规程是设计新建和扩建车间(工厂)的基础
1)确定生产需要的机床种类和数量
2)确定机床布置和动力配置
3)确定车间面积
4)确定工人的工种和数量
(四)机械加工工艺规程的格式
图1-4为机械加工的工艺过程卡片
1-4为机械加工的工艺过程卡片 |
图1-5为机械加工工序卡片
图1-5为机械加工的工艺过程卡 |
四.机械加工工艺规程的设计原则、步骤和内容
(一)机械加工工艺规程的设计原则
1.必须可靠地保证零件图纸上所有技术要求的实现。
2.在规定的生产纲领和生产批量,一般要求工艺成本最低。
3.充分利用现有生产条件,少花钱,多办事。
4.尽量减轻上人的劳动强度,保障生产安全,创造良好、文明的劳动条件。
(二)设计机械加工工艺规程的步骤和内容
1.阅读装配图和零件图
了解产品的用途、性能和工作条件,熟悉零件在产品中的地位和作用。
2.工艺审查
审查图纸上的尺寸、视图和技求要求是否完整、正确、统一,找出主要的技术要求和分析关键的技术问题;审查零件的结构工艺性。
零件的结构工艺性:
是指在满足使用要求的前提下制造该零件的可行性和经济性。功能相同的零件,其结构工艺性可以有很大差异。所谓结构工艺性好,是指在现有工艺条件下既能方便制造,又有较低的制造成本。
举例说明零件的结构工艺性:
3.熟悉或确定毛坯
确定毛坯的主要依据是零件在产品中的作用和生产纲领以及零件本身的结构。
毛坯的种类:铸件、锻件、型材、焊接件、冲压件等
4.拟订机械加工工艺路线
1)定位基准的选择
2)加工方法的确定
3)加工顺序的安排
4)热处理、检验及其他工序的安排
5.确定满足各工序要求的工艺装备(机床、刀具、夹具、量具)对需要改装或重新设计的专用工艺装备应提出具体的设计任务书。
6.确定各主要工序的技术要求和检验方法
7.确定各工序的加工余量、计算工序尺寸和公差
8.确定切削用量
9.确定时间定额
10.填写工艺文件
第三节 工艺路线的制定
一.定位基准的选择
(一)粗基准的选择
1.粗基准:
未经机械加工的定位基准称为粗基准。机械加工工艺规程中第一道加工工序所采用的定位基准都是粗基准。
举例说明粗基准的选择对零件加工的影响
2.选择原则
1)保证相互位置精度要求的原则
如要保证工件上加工面与不加工面的相互位置要求,应以不加工面为粗基准。如图所示。
2)保证加工表面加工余量合理分配的原则
如要首先保证工件某重要表面的余量均匀,应选择该表面的毛坯面为粗基准。
3)便于工件装夹的原则
选择粗基准时,必须考虑定位准确,夹紧可靠以及夹具结构简单、操作方便等。这样要求选用的粗基准尽可能平整、光洁和足够大的尺寸,不允许有锻造飞边,浇铸浇口,或其他缺陷。
4)粗基准一般不得重复使用的原则
若能采用精基准定位,粗基准一般不应被重复的使用
(二)精基准的选择
1.精基准:
以机械加工过的表面作为定位基准。
2.出发点:
保证设计技术要求的实现以及装夹准确、可靠、方便。
3.选择原则
1)基准重合原则:
尽可能的选择被加工表面的设计(工序)基准为精基准
2)基准统一原则:
工件以某一精基准定位,可以比较方便的加工大多数或所有其他表面,则应尽可能的把这个基准面加工出来,并达到一定精度,以后工序均以它为精基准加工其他表面。
在实际生产中,经常使用的统一基准形式有:
1)轴类零件常使用两顶尖孔作统一基准;
2)箱体类零件常使用一面两孔(一个较大的平面和两个距离较远的销孔)作统一基准;
3)盘套类零件常使用止口面(一端面和一短圆孔)作统一基准;
4)套类零件用一长孔和一止推面作统一基准。
采用统一基准原则好处:
1)有利于保证各加工表面之间的位置精度;
2)可以简化夹具设计,减少工件搬动和翻转次数。
★注意:
采用统一基准原则常常会带来基准不重合问题。此时,需针对具体问题进行具体分析,根据实际情况选择精基准。
3)互为基准原则
4)自为基准原则
5)便于装夹原则——所选择的精基准,应能保证工件定位准确、可靠,并尽可能使夹具结构简单、操作方便。
二.加工经济精度与加工方法的选择
(一)加工经济精度
在正常加工条件下(采用符合质量标准的设备和工艺装备,使用标准技术等级工人,不延长加工时间),一种加工方法所能保证的加工精度和表面粗糙度
各种加工方法所能达到的加工精度和表面粗造度,都是在一定的范围内的。任何一种加工方法只要精心操作、细心调整、选择合适的切削用量,加工精度就可以提高,表面粗造度就可以减小,但所耗费的时间与成本也会愈大。
(二)加工方法的选择
1.根据每个加工表面的精度要求,(尺寸、形状、位置、精度及表向粗造度对照各种加工方法能达到的精度及粗糙度,选择最合理的加工方法。
例:加工一直经φ35H7▽0.8的孔
a.钻孔→扩孔→铰
b.钻孔→拉
c.钻孔→粗镗→半粗镗→精镗
根据工件加工表面特点和产量决定采用哪一种方法
各种加工方法能达到的要求参考P31-35.表1-13.1-14.1-15.1-16
2.加工材料的性质:
如淬火钢专用磨削,有色金属常用金刚镗或者高速精密车削
3.考虑生产类型:
即生产率和经济性问题。在大批大量生产中可用专用高效设备,如平面和孔可采用拉削加工代替铣、刨、镗。
4.考虑本厂(本车间)的现有设备及技术要求,能达到的加工经济精度。
三.典型表面的加工路线
(一)外圆表面的加工路线
1.粗车→半精车→精车:
应用最广,满足IT≥IT7,▽≥0.8外圆可以加工
2.粗车→半精车→粗磨→精磨:
用于有淬火要求IT≥IT6,▽≥0.16的黑色金属。
3.粗车→半精车→精车→金刚石车:
用于有色金属、不宜采用磨削加工的外用表面。
4.粗车→半精车→粗磨→精磨→研磨、超精加工、砂带磨、镜面磨、或抛光在2的基础上进一步精加工。
目的为了减少粗糙度,提高尺寸精度,形状和位置精度。
(二)孔的加工路线
1.钻→粗拉→精拉:
用于大批大量生产盘套类零件的内孔,单键孔和花键孔加工,加工质量稳定,生产效率高。
2.钻→扩→铰→手铰:
用于中小孔加工,扩孔前纠正位置精度,铰孔保证尺寸、形状精度和表面粗糙度。
3.钻或粗镗→半精镗→精镗→浮动镗或金刚镗
应用:
1)单件小批量生产中箱体孔隙加工。
2)位置精度要求很高的孔系加工。
3)直径比较大得孔ф80mm以上,毛坯上已有铸孔或锻孔。
4)有色金属有金刚镗来保证其尺寸,形状和位置精度以及表面粗糙度的要求
4./钻(粗镗)粗磨→半精磨→精磨→研磨或衍磨
应用:淬硬零件加工或精度要求高的孔加工。
说明:
1)孔最终加工精度很大程度上取决于操作者的水平。
2)特小孔加工采用特种加工方法。
(三)平面的加工路线
1.粗铣→半精铣→精铣→高速铣
平面加工中常用,视被加工面精度和表面粗糙度技术要求,灵活安排工序。
2./粗刨→半精刨→精刨→宽刀精刨、刮研或研磨
应用广泛,生产率低,常用于窄长面的加工,最终工序安排也视加工表面的技术要求而定。
3.铣(刨)→半精铣(刨)→粗磨→精磨→研磨、精密磨、砂带磨、抛光
加工表面淬火,最终工序视加工表面的技术要求而定。
4.拉→精拉
大批量生产有沟槽或台阶表面。
5.车→半精车→精车→金刚石车
有色金属零件的平面加工。
四.工序顺序的安排:
(一)工序顺序的安排原则
1.先加工基准面再加工其他表面:
先基面后其他
1)工艺路线开始安排的加工面应是选作定位基准的精基准面,然后再以精基准定位加工其他表面
2)为保证一定的定位精度,当加工面的精度要求高时,精加工前一般应先精修一下精基准。
2.加工平面后加工孔:
先面后孔
1)零件有较大平面可作为定位基准时,先加工定位面,以面定位加工孔。
2)毛坯面上钻孔钻夹易偏,若该平面需要加工则在钻孔前加工。
3.加工主要表面,后加工次要的表面:
先主后次
4.安排粗加工工序,后安排精加工工序
先粗后精
(二)热处理工序及表面处理工序
1.为改善切削性而进行的热处理工序(退火、正火、调质)→(预备热处理)用于切削加工前。
2.为了消除内应力而进行的热处理(人工时效、退火、正火)安排用于粗加工之后。
3.为改善材料力学物理性质,半精加工后精加工前安排淬火。淬火→回火→渗碳淬火等热处理工序。
4.精密零件在淬火后安排冷处理以稳定零件尺寸。
5.提高零件表面耐磨性或耐腐蚀性而安排的热处理工序,以及以装饰为目的而安排的热处理工序(镀铬、阳极氧化、镀锌、发蓝)一般放在工艺过程最后。
(三)其他工序的安排
1.检验工序:
1)零件加工完毕之后
2)从一车间转到另一车间前后
3)关键工序的前后
2.一般尺寸检验、X射线、检查、超声波探伤等用于工件内部的质量检查,一般安排在工艺过程的开始。
磁力探伤、荧光检验用于工件表面质量的检验,在精加工前后进行,。
密封性检验、零件平衡、零件的重量检验、在工艺过程最后进行。
3.去毛刺处理在切削加工后,装配工件前安排情况
4、清洗工件一般安排在进入装配之前。
五.工序的集中与分散
1、工序集中
使每个工序中包括尽可能多的工步内容,从而使总的工序数目减少
优点:
1)有利于保证工件各加工面之间的位置精度;
2)有利于采用高效机床,可节省工件装夹时间,减少工件搬运次数;
3)可减小生产面积,并有利于管理。
2、工序分散
使每个工序的工步内容相对较少,从而使总的工序数目较多
工序分散优点:
每个工序使用的设备和工艺装备相对简单,调整、对刀比较容易,对操作工人技术水平要求不高
3、工序集中与工序分散的应用
传统的流水线、自动线生产,多采用工序分散的组织形式(个别工序亦有相对集中的情况)。
多品种、中小批量生产,为便于转换和管理,多采用工序集中方式。
由于市场需求的多变性,对生产过程的柔性要求越来越高,工序集中将越来越成为生产的主流方式。
六.加工阶段划分的原因
(一)划分加工阶段的原因
1.粗加工时,切削余量大、切削热量大、工艺系统受力变形及内应力变形存在而无法消除。要在后续阶段逐步减少切削用量,逐步修正工件误差,阶段之间时间间隔用于自然时效,有利于工件消除内应力和部分变形。
2.后续工序易把以加工好的加工面划伤。
3.不利于及时发现毛坯的缺陷。
4.不利于合理使用设备。粗加工采用普通机床,精加工采用精密机床。
5.不利于合理使用技术工人。
(二)划分方法
1.粗加工阶段:
提高生产率、去除加工面的大部分余量。
2.半精加工阶段:
减少粗加工留下的误差,使加工面达到一定的精度,为精加工做准备。
3.精加工阶段:
保证工件的尺寸、形状和位置精度达到或基本达到图纸规定的精度要求及表面粗糙度要求。
4.精密、超精密或光整加工阶段:
对精度要求很高的工件,在工艺过程的最后安排珩磨、研磨、精密磨、超精加工、金刚车、金刚镗或其它特种方法加工,以达到最终的精度要求。
中间热处理中间,自然把加工工艺过程分为几个加工阶段。
第四节加工余量、工序间尺寸及公差的确定
一.加工余量的概念
余量的大小对零件的加工余量和生产率有较大影响。余量大会增大机加工劳动量,降低生产率,增加材料、工具、能源消耗、提高成本,余量小又不能消除前道工序留下的误差及其表面缺陷,甚至产生废品。因此必须合理确定加工余量。
(一)加工总余量(毛坯余量)与工序余量
1.加工总余量:
毛坯尺寸与余零件设计尺寸之差,其大小取决于加工过程中每个工序切除金属层厚度的总和。
2.工序余量:
每一工序所切除的金属层厚度称为工序余量。
加工总余量和工序余量之间的关系用下式表示:
Z0=Z1+Z2+Z3+…+Zn=
3.单边余量:
零件非对称结构的非对称表面,其加工余量一般为单边余量。如平面、端面、
槽深余量,为实际切除金属层厚度
Zi=Li-1-Li
Zi——本工序余量
Li-1——上工序基本尺寸
Li——本工序的基本尺寸
4.双边余量:
零件对称结构的对称表面,其加工余量一般为双边余量
如:内外圆柱面和回转体表面
2Zi=di-1-di(外圆表面)
2Zi=Di-1-Di (内圆表面)
5.余量公差:
工序尺寸有公差,所以加工余量也必然在某一公差范围内变化,其公差大小等于本道工序尺寸公差与上道工序尺寸公差之和。
TZ=Zmax-Zmin=Tb+Ta
TZ——工序余量公差
Zmax——工序最大余量
Zmin——工序最小余量
Tb——本道工序的工序尺寸公差
Ta——上道工序的工序尺寸公差
Zb——工序基本余量
6.一般情况下,工序尺寸按“入体原则”标注。
1)轴(被包容尺寸):指实体尺寸。
例如:轴的外径,长方体的长、宽、高。
其最大尺寸作为工序尺寸的基本尺寸(公称尺寸),上偏差为零。
表示为:
2)孔(包容尺寸):指非实体尺寸。
例如:孔的直径,槽的宽度。
其最小尺寸作为工序尺寸的基本尺寸(公称尺寸),下偏差为零。
表示为:
这样表示,是为了使工件以公称基本尺寸为目标尺寸加工时,仍有可切除量,避免过切产生废品。
3)毛坯尺寸则按双向对称偏差的形式标注。
表示为:
二.工序余量的影响因素
第一道粗加工工序余量与毛坯制造精度有关。毛坯制造精度高则第一道粗加工序加工工序余量小,毛坯制造精度低则第一道粗加工工序的加工余量就大。其它工序的工序余量的影响因素有以下几个方面:
1.上工序的尺寸公差Ta:
本工序应切除上道工序尺寸公差中包含的各种可能产生的误差。
2.上道工序产生的表面粗糙度Ry和表面缺陷层深度Ha:
3.上工序留下的需单独考虑的空间误差εa:
这些误差可能是上工序加工方法带来的,也可能是热处理后产生的,也可能是毛坯带来的。
4.本工序的装夹误差εb:
定位误差和夹紧误差。此项误差直接影响被加工表面和切削刀具的相对位置,所以加工余量中应该包括此项误差
5.余量计算公式
单边:
双边:
三.加工余量的确定
1.计算法:
用于在影响因素清楚的情况下采用,且不能离开具体的加工方法和条件,要具体情况具体分析。
2.查表法:
以工厂生产实践和实验研究积累的经验所制成的表格为基础,并结合实际情况加以修正,确定加工余量。此法方便、迅速、应用广泛。
3.经验法:
有一些有经验的工程技术人员或工人根据经验确定加工余量的大小。
四.工序尺寸公差的确定
(一)基准重合时工序尺寸与公差的确定
1.确定各加工工序的加工余量
2.从最后工序开始,即从设计尺寸开始到第一道加工工序,逐次加上每道加工工序余量,得各工序基本尺寸(包括毛坯尺寸)。
3.除最后工序,其余工序按各自所采用加工方法的加工精度确定工序尺寸公差。
4.按入体原则标注工序尺寸
【例1】:
某轴的直径为,其尺寸精度为IT5,表面粗糙度要求为,要求高频淬火,毛坯为锻件,工艺路线为:
粗车—半精车—高频淬火—粗磨—精磨—研磨
计算各工序的工序尺寸和公差
1)查表确定加工余量:
研磨余量0.01mm,
精磨余量0.1mm,
粗磨余量0.3mm,
半精车余量1.1mm,
粗车余量4.5mm,
加工的总余量6.01mm,修正为6mm,
粗车余量修正为4.49mm。