中国轮胎循环利用现状 中国太阳能利用现状
1中国废旧轮胎回收市场概况随着国民经济的快速发展和人民生活水平逐步提高,我国已成为橡胶资源消费大国。目前,我国年均橡胶消耗量占世界橡胶消费总量的30%,每年我国橡胶制品工业所需70%以上的天然橡胶、40%以上的合成橡胶需要进口,供需矛盾十分突出,橡胶资源短缺对国民经济发展的影响日益显现。
轮胎是我国最主要的橡胶制品。2009年,我国生产轮胎消耗橡胶已占全国橡胶资源消耗总量的70%左右,年产生废轮胎2.33亿条,重量约合860万吨,折合橡胶资源约300多万吨,若能全部回收再利用,相当于我国5年的天然橡胶产量。
由上图可看出,我国废旧轮胎利用率约为95%,但环保型加工再利用率却很低。由于我国橡胶资源短缺,传统的废轮胎生产再生胶仍是主要加工利用的方法。近些年,随着我国石油、能源价格不断上涨,废轮胎土法炼油已迅速发展成为一个破坏环境的畸形产业。
2目前我国废旧轮胎综合利用途径 目前我国废旧轮胎综合利用的途径大致有5种:
⑴ 旧轮胎翻新
翻胎工业是橡胶工业的一个重要组成部分,又是资源再生利用环保产业的组成部分。旧轮胎翻新不仅可延长轮胎使用寿命、节约能源、节约原材料、降低运输成本,而且减少环境污染。
⑵ 生产再生胶粉
这是一门新兴材料科学,是集环保与资源再生利用为一体的很有发展前途的回收方式,也是提倡发展循环经济的最佳利用形式。再生胶粉可被应用到防水卷材料、轮胎和胶粉改性沥青的生产。
⑶ 热 解
废轮胎在高温下分离提取燃气、油、炭黑、钢铁,或直接热能利用等,由于投资及二次污染问题,这种回收利用方式在国内发展较慢。
目前以色列TDE公司研发将废旧轮胎作为燃料生产电能的新型系统,这种系统在燃烧产生电能出售给国家电网的系统,同时还能产生市场需要的副产品,如钢材,硫、干冰等。整个过程中产生的气体和副产品都是清洁和安全的,对环境无污染。该处理工艺可在国内推广。
⑷ 生产再生橡胶
再生胶能部分地代替生胶用于橡胶制品,以节约生胶及炭黑,也有利于改善加工性能及橡胶制品的某些性能。
⑸ 废旧轮胎原形直接利用。
用作港口码头及船舶的护舷、防波护堤坝、漂浮灯塔、公路交通墙屏、路标以及海水养殖渔礁、游乐游具等,但使用量不到废轮胎量的1%。
3我国轮胎翻新与循环利用行业发展概况 “十一五”期间我国轮胎翻新与循环利用行业实现了稳步发展,主要表现在:生产规模不断扩大,产业布局日趋合理,生产技术水平不断提升,产品品种不断增加,环保意识不断增强。从事废旧轮胎循环利用的企业已由2005年年末的1400余家发展到2009年末的2000余家。
2009年轮胎翻新量为1300万条,与2005年相比增长幅度为75%,比“十一五”发展规划预测的1763万条减少463万条;再生胶产量270万吨,比“十一五”发展规划预测的140万吨增加130万吨;橡胶粉产量20万吨,比“十一五”发展规划预测的80万吨减少60万吨;热解5万吨。
“十一五”后期,我国载重汽车轮胎翻新开始大多采用预硫化胎面翻新法,已形成比较完善的工业体系;工程轮胎翻新已由仅用无模刻花的翻新法翻新巨型工程子午线轮胎,发展到可用活络模法甚至预硫化胎面法翻新;轮胎翻新设备基本上采用了机电一体化,计算机数控脉冲、无刷电机、滚珠丝杠传动技术的应用,使加工精度大为提高,已基本达到国际上现代轮胎翻新设备制造的水平;轮胎翻新的无损检测设备已发展到品种基本齐全。
4行业发展现状及面临的形式 我国是橡胶资源十分匮乏的国家,随着汽车工业和矿山及工程机械制造业的迅猛发展,我国橡胶消耗量已连续八年居世界首位,每年70%以上的天然橡胶和40%的合成橡胶依靠进口,供需矛盾十分突出。据测算,2009年我国废轮胎产生量2.33亿条,约合重量860万吨,折合橡胶资源300多万吨;倘若有效地回收再利用这部分资源,相当于节约我国天然橡胶5年的总产量。《国民经济和社会发展第十一个五年规划纲要》中明确提出要将轮胎翻新再制造等列入循环经济示范试点工程,并将“落实节约资源和保护环境”作为我国的又一项基本国策;
政府的一系列政策导向,旨在进一步推进废旧轮胎资源的再利用,降低橡胶资源消耗量,缓解其供需矛盾。如何进一步做好废旧轮胎资源综合利用工作,最大限度地提高其无害化利用率,是建立资源节约型和环境友好型社会的一个集中体现,是功在当代、利在千秋的系统工程。
目前我国在废旧轮胎资源综合利用方面已形成了四大业务板块;一是旧轮胎翻新再制造;二是废轮胎生产再生胶;三是废轮胎生产橡胶粉;四是废轮胎热解。初步创建了具有中国特色的废旧轮胎循环利用工业体系。
⑴ 行业发展态势
a、生产规模不断扩大
截止2009年末,全国从事旧轮胎翻新和废轮胎加工利用的生产企业已达到2000余家。一个以废旧轮胎为主要生产原料的资源节约型产业已初具规模,已初步形成了旧轮胎翻新、废轮胎生产再生胶、橡胶粉及热解的完整产业链。
b、产业布局日趋合理。
从生产企业分布来看,除我国西藏外,各省市区都分布有轮胎翻新和循环利用的生产企业,且呈集群式发展的态势,所加工的翻新轮胎产品已逐步被社会认可并得到广泛使用,再生橡胶、橡胶粉已成为不可或缺的第三橡胶资源。
c、生产技术水平不断提升
在生产设备上,轮胎翻新、再生橡胶、橡胶粉和热解生产所需的关键设备已由原来主要依靠进口到现今基本实现国产化,而且大多数产品已接近或达到国际先进水平,部分产品已出口美国等发到国家。在生产技术和生产方式上,轮胎翻新已由热翻斜交台为主改变为以预硫化法冷翻子午胎为主;常温精细胶粉生产技术已处于国际先进水平;再生胶生产企业已基本淘汰了油法、水法等落后工艺,常压连续塑化技术、高温连续再生工艺、加压捏炼法以及“水煮法”等技术已为再生胶无害化生产探索出新路子;再生橡胶脱硫技术逐步向低能耗、低排放方向发展;丁基再生橡胶生产技术已实现工业化生产;降温负压催化热解技术的应用,正在开创将废轮胎资源“吃干榨净”的新方法。
d、产品品种不断增加
轮胎翻新企业已由过去单纯的翻新汽车轮胎,扩展到翻新矿山工程轮胎和航空轮胎;再生橡胶产品已有轮胎类、特种类、专用类等八大系列三十多个品种。特别是复原橡胶、无嗅味环保型再生橡胶的研制成功,不仅满足了国内市场需求,而且出口国际市场;橡胶粉也在向直接利用和橡胶粉改性沥青的应用方面拓展。
e、环保意识有所增强
大部分大型再生橡胶生产企业基本实现了对生产过程中的废钢丝、废纤维的有效利用,实现了废渣零排放;对冷却用水进行循环利用,力争实现废水零排放;对生产中的尾气,通过生物法、化学法、循环法等进行有效综合治理。但仍有部分生产经营者环保意识淡薄,受利益驱动,以破坏环境为代价,有令不行、有禁不止,继续从事土法炼油生产,对资源与环境造成灾难性破坏。
⑵ 行业存在的主要问题
a、由于相关的法律、法规和产业政策不够完善,国家标准和行业标准也不够健全,加之行业没有强有力的监管等诸多因素,致使废轮胎的回收、加工处理、再利用处于自由发展态势,导致了行业的无序发展和企业的运营困难。这也是造成我国橡胶资源浪费和二次环境污染的主要原因。
b、由于国家对新轮胎可翻新性能的要求没有纳入强制性技术标准,可翻新的旧轮胎资源严重短缺,废旧轮胎生成比例严重失衡,废轮胎与旧轮胎的比例为95:5,可翻新旧轮胎仅占废旧轮胎的5%,与发达国家废旧轮胎55:45的比例及45%的轮胎翻新率相差甚远。
c、废轮胎回收体系不健全。目前我国还没有建立规范的废轮胎回收体系,90%以上废轮胎是由民间个体自发收购自由交易。废轮胎回收后不能完全进入正规加工处理企业,给土法炼油和小再生橡胶生产提供了原料来源;而回收经营者的无序竞争,一方面使得有限的废轮胎资源得不到规范、合理地回收利用,另一方面层层倒卖和转运即浪费了运输资源,又推高了废轮胎回收的市场价格。
d、旧轮胎翻新和废轮胎综合利用企业普遍生产规模较小、产业化程度较低。目前国内轮胎翻新、再生橡胶、橡胶粉及热解生产的四个专业,基本没有能够引领产业化发展趋势的大型龙头企业。现有的大多数企业生产技术和管理方式相对较落后,在市场上各自为政,没有形成产业规模,不仅难以参与国际市场竞争,而且很难实现大的跨越式发展。
e、生产经营方式粗放,节能减排指数较低。受市场和利益的驱动,“三小”企业(小翻胎、小再生胶、小橡胶粉)依靠落后的生产技术和工艺,采取低成本、低价格和低附加值的粗放式生产经营模式,形成高能耗、高排放的现状,对市场秩序形成冲击;特别是土法炼油屡禁不止,2008年消耗废轮胎约400万吨,已成为我国废轮胎利用的“第一大产业”。
f、科技人才奇缺。作为低碳经济和人类“希望工程”的再生资源产业,在我国尚无一所专门从事其研究的高等院校或国家级科研机构,很多基本的理论问题和关键的技术问题得不到及时解决。全行业职工平均文化程度偏低,业内一批知名的老专家也年逾古稀,因此研发机构、技术人才和技术更新问题已成为本行业实现跨越式发展的羁绊,急需建立轮胎翻新、再生橡胶、橡胶粉及热解等四方面的“国家级技术研发中心”,以带动行业的科技开发和人才培养。
3.2市场预测
3.2.1轮胎翻新行业市场预测
1、翻新轮胎的优点
预硫化轮胎(冷翻胎)与新轮胎相比,有以下几方面的优点
⑴节约成本:在良好的使用与保养条件下,一条轮胎可以多次进行预硫化翻新。具体地说,尼龙帘线轮胎可翻新2~3次,钢丝子午线轮胎可翻新3~6次。每翻新一次,可重新获得相当于新轮胎60%~90%的使用寿命,平均行驶里程大约为5~7万km。通过多次翻新,至少可使轮胎的总寿命延长2~3倍。
而翻新一条废旧轮胎所消耗的原材料只相当于制造一条同规格新轮胎的15%~30%,价格仅为新轮胎的20%~50%。质量合格的翻新胎也可以按照新胎同样的合法速度行驶,在安全、性能和舒适程度上不亚于新胎。
⑵ 节能:生产每条新轮胎约需970MJ能源,翻新轮胎仅需400MJ。
⑶ 节约原材料:生产每条新轮胎需要约83.27L的石油,翻新轮胎仅需要26.5L。
⑷ 减排:每条翻新轮胎比新轮胎减少二氧化碳排放26.4kg。
⑸ 延长使用寿命:每翻新一次,可重新获得相当于新轮胎60%-90%的使用寿命,平均行驶里程5-7万km。通过多次翻新,至少可使轮胎的总寿命延长2-3倍。因此,发达国家非常重视轮胎翻新和再使用。2005年美国只有18家轮胎制造商,48家轮胎生产厂,但轮胎翻新厂或销售商有1094家,年翻新轮胎约3200万条,翻新率10.7%。
⑹ 安全:质量合格的翻新轮胎是安全可靠的。翻新轮胎被广泛应用与民航、美国军用飞机、学校大巴和各种急救车,汽车运输公司已基本依靠翻新轮胎用于运输。经实践证明,翻新轮胎与新轮胎一样安全可靠和经久耐用。
2、轮胎翻新的市场潜力
工业和信息化部的统计数据显示,发达国家的轮胎翻新比例在45%以上,轮胎翻新已经成为发达国家处理废旧轮胎的主要手段之一。来自纽耶拉国际贸易(上海)有限公司的统计数据显示,目前世界上发达国家的翻胎比例相当高,与新胎达到1:1的水平。如美国每年的新胎用量约为1600万条,翻新胎约为1700万条左右。
而目前我国轮胎翻新产量约为1400万条,轮胎翻新率不足5%,这与汽车产销量、轮胎产量世界第一大国的地位极不相称。很大原因在于,轮胎翻新产业面临胎体过度使用的资源性短缺和降标或非标加工问题,严重制约和影响了我国轮胎翻新产业的整体发展水平。由于可翻胎资源缺乏,不少企业常常处于“等米下锅”的状态,加之割标、改标、不“三包”轮胎的大肆泛滥,翻胎行业正面临灭顶之灾。
但也正是由于这些因素,我国的轮胎翻新业也同时具有很大的发展潜力与优势。有专家估计,如果替换胎市场40%均使用翻新轮胎,那么我国每年的轮胎翻新量将达到6000万条,是目前翻胎产量的4~5倍。国际轮胎、翻胎企业也因为看好中国翻胎产业的发展前景,正在加快布局中国翻胎市场。
根据《废旧轮胎综合利用指导意见》发展目标,到2015年,到2015年,国内旧轮胎翻新水平有较大提高。载重轮胎翻新率提高到25%,巨型工程轮胎翻新率提高到30%,轿车轮胎翻新实现零的突破。
3.2.2胶粉行业预测
目前国内废旧轮胎再生胶粉主要用于三个领域:
⑴ 防水卷材料
1986年,苏联将胶粉成功地应用于橡胶沥青防水卷材、无机绝缘片材和三层板材组成的隔音复合地板等建筑材料。20世纪90年代以来,我国北方地区开始把粗胶粉应用于低档防水卷材。科研试验表明,在橡胶沥青防水卷材中加入精细胶粉,可以部分或全部取代SBS(苯乙烯类热塑性弹性体),每取代1吨SBS,每平方米防水卷材就可节约0.5~1.5元。此外,精细胶粉还可应用于聚氨酯防水材料砖的生产,同样能降低成本、提高质量,综合经济效益非常显著。
⑵ 橡胶制品及轮胎生产
2009年国内废旧轮胎精细胶粉市价2500~3500元/吨,天然橡胶市价14000元~16000元/吨,两者相比废轮胎胶粉价格极具具竞争力,每替代一吨天然橡胶,成本可降低10000元~12000元。
⑶ 胶粉改性沥青
用胶粉改性沥青铺设的公路,与普通路面相比,可延长使用寿命1-3倍,降低噪音50%-70%,提高路面的耐热、耐寒性(80℃高温不软,-35℃低温不裂),增强防滑性进而缩短刹车制动距离,提高了安全系数,特别适用于建造高速公路。目前国内使用的主要是SBS改性沥青,2007年国内产量约1500万吨,进口420万吨。2009年国内生产的SBS沥青改性剂市场售价20000元/吨,而同类型胶粉改性剂能降低成本30%左右,使之取代目前市场主导的SBS改性沥青成为历史的必然。
然而由于价格昂贵且无交通部的大力支持,改性沥青一直无法在我国得到广泛的推广。许多发达国家为推广胶粉改性沥青的应用相继立法,如美国立法规定:凡国家投资或资助的道路建设必须采用胶粉改性沥青,并且规定胶粉的使用量必须达到20%以上。目前美国铺设的胶粉改性沥青路面已逾万公里。
根据《废旧轮胎综合利用指导意见》发展目标,到2015年,我国废旧轮胎资源环保达标率达到80%以上,橡胶粉年产量达到100万吨以上。
3.2.3再生胶市场预测
中国是一个生胶资源相对紧缺的国家,中国每年再生胶消耗量的50%左右需要进口。目前国内生产再生橡胶能力超过500万吨,2009年产量约270万吨;再生橡胶企业数量约1500家,主要分布在河北、山西、江苏、浙江、山东、河南、四川等地。再生胶生产企业年产量达到万吨以上的已超过100家,5万吨以上的生产企业已超过10家,区域性规模生产能力基本都达到10万吨左右。
中国再生橡胶工业在生产规模、企业规模、品种档次、工艺技术、装备配套、出口创汇等方面均已达到世界先进水平。继20世纪80年代成为全球最大再生橡胶生产国之后,中国已跻身全球再生橡胶工业发达国家行列。
再生胶能部分地代替生胶用于橡胶制品,以节约生胶及炭黑,也有利于改善加工性能及橡胶制品的某些性能。
根据《废旧轮胎综合利用指导意见》发展目标,到2015年,我国废旧轮胎资源环保达标率达到80%以上,再生胶年产量达到300万吨以上。
3.3中国废旧轮胎综合利用行业发展趋势
废旧轮胎资源循环利用作为朝阳产业,已逐步成为人们的共识。世界各国,特别是发达国家和地区都十分重视旧轮胎的翻新再利用,而且发达国家已将其作为节约橡胶资源的重要产业。旧轮胎预硫化翻新加工过程无“三废”排放,是绿色环保行业,不仅可以节约大量橡胶、钢丝、石油能源等资源,而且又可以实现废旧轮胎的减量化、再利用和资源化。
在近两年国际金融危机大背景下,虽然一度给我国废旧轮胎资源循环利用行业带来了较大的冲击,但在国家及时采取扩大内需、保增长、促发展政策的指引下,加之汽车运输业的持续增长,使我行业在不利的国际经济环境下依然保持着总体增长的态势。
展望未来,废旧轮胎资源综合利用这样一项功在当代,利在千秋的伟业,已经日益受到政府和社会各界的高度重视,一系列扶持政策的出台,必将对中国的废旧轮胎循环利用产业发展带来巨大的机遇。
中再交易网参考观点
我国再生橡胶行业是伴随着轮胎行业的快速发展而发展的,废轮胎是再生橡胶生产企业的主要原料,占总利用量的60%~70%。同样,绿色轮胎行业的发展也需要再生橡胶生产企业的支持,再好的轮胎经过几次翻新后终究要废弃,成为黑色污染,影响环境,绿色意义也必须大打折扣,再生橡胶和胶粉可作为新型环境保原料应用于绿色轮胎生产,有效降低轮胎制造成本,节约资源,并赋予绿色轮胎更丰富的内涵,因此,绿色轮胎与再生橡胶的发展是相辅相存、互利双赢的关系,只有加强合作,才能共同发展。
原文题目:我国轮胎循环利用现状
更多阅读
中国轮胎循环利用现状 中国太阳能利用现状
1中国废旧轮胎回收市场概况随着国民经济的快速发展和人民生活水平逐步提高,我国已成为橡胶资源消费大国。目前,我国年均橡胶消耗量占世界橡胶消费总量的30%,每年我国橡胶制品工业所需70%以上的天然橡胶、40%以上的合成橡胶需要进口,供需
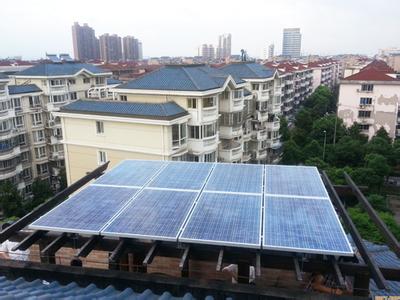
太阳能产业 中国太阳能热利用产业仍健康发展
2012年,在整体经济大环境不景气的条件下,有关鼓励政策推陈出新,市场也发生了变化,消费者需求呈多样化趋势,不少中小太阳能热利用企业由于没能做好转型升级工作,对行业发展趋势缺乏清晰认识,出现了发展增速减缓或者下滑现象。近
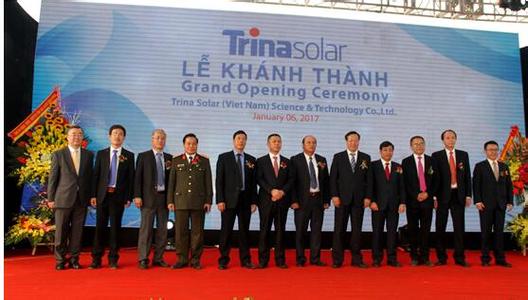
表彰优秀员工主持词 2011年中国太阳能热利用行业优秀企业表彰
2011年中国太阳能热利用行业优秀企业表彰名单揭晓 为了总结“十一五”期间行业成就,实现“十二五”规划目标的全面
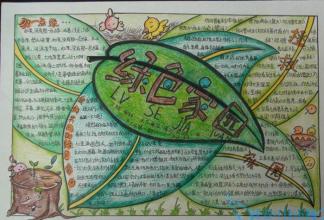
绿色循环低碳方案 莫和克低碳循环利用绿色地毯
来自美国的全球领先的家居及商业地毯制造商及销售商美国莫和克集团近日向中国用户介绍了其享誉盛名的“绿色地毯”理念。莫和克集团总裁AlKabus先生在“绿色地毯-实用可持续发展策略”的研讨会上表示,作为地毯行业最大的循环回收企

蓄电池报废 中国每年报废5000万只蓄电池 循环利用大有可为
促进环保,发展新能源是当今世界的发展潮流。现在国内仅蓄电池一年就报废5000多万只,而且这个数字每年仍以30%的速度增长。 据日前召开的北京旧铅酸蓄电池修复循环利用技术推广会透露,中国每年报废的5000多万只铅酸蓄电池有望得